How long does it take to build a tiny house? This journey into the miniature world of homes unveils a captivating dance between design, resources, and time. The process, from initial concept to final finish, is a testament to both the ingenuity and the constraints of crafting a compact, yet complete, living space.
Factors like the complexity of the design, the chosen materials, and the builder’s experience significantly impact the overall construction timeline. This exploration delves into the intricacies of tiny house construction, revealing the range of times involved and the factors that influence them.
Defining “Tiny House”
A tiny house represents a departure from conventional housing, prioritizing minimalist living within a compact footprint. Its defining characteristic is its significantly smaller size compared to traditional homes, often resulting in a unique and intentional lifestyle choice. This smaller scale necessitates careful consideration of space optimization and material selection.The concept of a tiny house encompasses a wide range of designs and construction methods, each reflecting the owner’s priorities and the surrounding environment.
This section delves into the key characteristics of tiny homes, contrasting them with traditional construction and exploring the diverse types of tiny houses available.
Size Parameters and Typical Features
Tiny houses are characterized by their compact dimensions, typically ranging from 80 to 400 square feet. This deliberate reduction in size encourages mindful consumption and prioritizes essential living areas. Typical features include a kitchen, bathroom, and sleeping area, often integrated and designed for efficiency. Built-in storage solutions and multi-functional furniture are common design elements. The size constraints, however, necessitate innovative layouts and compact appliances.
Materials Used in Construction
A wide variety of materials are employed in tiny house construction. Common choices include sustainable materials like reclaimed wood, metal, and composite materials. Reclaimed wood, for instance, offers an aesthetic appeal and environmental benefits. Metal, often used for exterior cladding, provides durability and resistance to the elements. Composite materials offer a balance of strength and affordability.
The selection of materials is frequently influenced by budget constraints and desired aesthetic.
Comparison with Traditional Home Building
Tiny house construction differs fundamentally from traditional home building in several key aspects. Traditional homes typically involve elaborate permit processes and adhere to stringent building codes, whereas tiny house construction often involves more streamlined processes and localized regulations. Construction timelines and labor costs can be significantly lower in tiny house projects, although specialized skills may be needed for unique designs.
Constructing a tiny haven, a testament to self-reliance, takes more than just bricks and mortar; it’s a journey of the soul. The meticulous process, like a well-crafted chicken piccata slow cooker recipe chicken piccata slow cooker recipe , requires patience and profound understanding of the materials, and a deep connection to the space you’re creating. Ultimately, the true measure of time spent isn’t in days or weeks, but in the harmony of intention and execution, revealing the true essence of what it takes to build a tiny house.
The design process for tiny houses emphasizes efficiency and adaptability, focusing on the functionality of each space.
Types of Tiny Houses
Tiny houses can be categorized by their foundation and construction method. Wheel-mounted tiny houses, often on trailers or towable platforms, offer high mobility and flexibility. Houses built on foundations, while more permanent, allow for greater customization and potential integration into existing landscapes. Some tiny houses feature unique design elements, such as solar panels for energy independence or water-saving fixtures.
Table: Types of Tiny Houses
Type of Tiny House | Typical Size Range (sq ft) | Common Materials | Estimated Construction Time (months) |
---|---|---|---|
Wheel-mounted | 100-300 | Plywood, Metal, Reclaimed wood | 3-6 |
Foundation-based | 150-400 | Concrete, Insulated Panels, Timber | 4-8 |
Solar-powered | 150-300 | Metal, Insulated Panels, Solar Panels | 4-7 |
Factors Influencing Construction Time
The construction time for a tiny house is significantly impacted by a multitude of interconnected factors. Careful consideration of these elements is crucial for realistic project planning and successful completion. Understanding these variables allows for better estimation of the timeframe required, enabling potential builders to proactively address potential delays and manage expectations.Design complexity, material selection, builder skill, and available resources all contribute to the overall construction duration.
Additionally, unforeseen circumstances and external factors like weather can extend the project timeline. This comprehensive analysis will explore the key influences on tiny house construction timelines, providing valuable insights for potential builders.
Design Complexity
The intricacy of the tiny house design directly correlates with the time required for construction. A simple, straightforward design with standard components will likely take less time than a highly customized or complex design featuring unusual architectural elements or bespoke features. The complexity of the design influences material cutting, assembly, and installation processes, which are critical in determining the overall construction duration.
Detailed blueprints and well-defined specifications are paramount to minimizing design-related delays.
Materials Used
The selection of building materials plays a significant role in the construction timeline. The availability, sourcing, and processing time for materials can significantly impact the project’s duration. For example, procuring rare or exotic woods, specialized insulation, or custom-fabricated components can add considerable time to the project. The complexity of the materials’ installation also influences the duration. Efficient material management and planning are essential for maintaining a timely construction process.
Builder Skill Level
The experience and skill level of the builder(s) directly affect the construction timeline. Experienced builders with a proven track record of successful tiny house projects will generally complete the construction process more efficiently. Conversely, less experienced builders may require more time for learning and perfecting techniques, potentially extending the project duration. Training, mentorship, and clear project documentation can mitigate this factor and optimize the construction process.
Available Resources, How long does it take to build a tiny house
The availability of necessary resources, including tools, equipment, skilled labor, and support personnel, significantly influences the construction timeline. Limited access to specialized tools or materials can result in delays. Sufficient manpower and efficient resource allocation are crucial for maintaining a steady pace of work. Efficient resource management can expedite the construction process and minimize delays.
Potential Delays
Unforeseen circumstances and external factors can lead to project delays. These can range from unexpected issues with material sourcing or quality control to unforeseen structural problems or adverse weather conditions. Material shortages, delays in delivery, or unforeseen structural issues can all contribute to significant project delays. Contingency planning is crucial to mitigate these potential delays and ensure project completion within a reasonable timeframe.
Maintaining clear communication channels with suppliers and subcontractors can minimize these disruptions.
Prefabricated vs. Custom-Built Tiny Houses
Prefabricated tiny houses often have shorter construction times compared to custom-built homes. The pre-fabricated nature of these structures means many components are pre-assembled off-site, reducing on-site construction time. In contrast, custom-built tiny houses, with their unique designs and specific requirements, necessitate more on-site work, which typically leads to a longer construction duration. This difference stems from the inherent customization involved in custom-built tiny houses.
Table: Factors Affecting Construction Time
Factor | Description | Estimated Impact on Timeline |
---|---|---|
Design Complexity | The intricacy of the design, including unique features and bespoke elements. | Significant impact; more complex designs extend the timeline. |
Materials Used | The availability, sourcing, and processing time of building materials. | Moderate to significant impact; sourcing delays can prolong the project. |
Builder Skill Level | Experience and proficiency of the builder(s). | Moderate impact; inexperienced builders may take longer to complete tasks. |
Available Resources | Access to tools, equipment, skilled labor, and support personnel. | Moderate impact; limited resources can lead to bottlenecks. |
Potential Delays | Unexpected issues with material sourcing, unforeseen structural problems, or adverse weather conditions. | Significant impact; delays can extend the timeline considerably. |
Prefabricated vs. Custom-Built | Comparison between pre-fabricated and custom-designed homes. | Prefabricated homes tend to have shorter construction times. |
Average Construction Timeframes
Construction timelines for tiny houses vary significantly based on design complexity, material choices, and the builder’s experience. Factors like permits, material availability, and unforeseen challenges can also impact the overall duration. Accurate estimations require careful consideration of these variables.Understanding the average construction timeframes is crucial for prospective tiny house owners to realistically plan their projects. This section explores typical timelines, considering different types of tiny houses and construction approaches.
Estimated Timeframes for Various Tiny House Types
A variety of factors influence the construction time for a tiny house, including size, complexity of the design, the materials used, and the experience level of the builder. Smaller, simpler designs using readily available materials generally require less time to complete than larger, more elaborate ones with custom features or exotic materials. The complexity of the structural design also plays a significant role, with intricate layouts and custom features lengthening the construction process.
Real-World Tiny House Project Durations
Numerous real-world examples illustrate the range of construction times. A tiny house built using prefabricated panels and a relatively straightforward design might be completed in a few weeks, while a custom-designed, off-grid home with intricate features could take several months. Documentation of actual projects, including detailed specifications, materials used, and the builder’s experience, is critical for establishing realistic expectations.
These records offer valuable insights into the factors that affect construction duration.
Comparison of Construction Times Across Builders
Comparing construction times across different tiny house builders or companies provides valuable insights into potential variations. Some builders specialize in streamlined construction methods, potentially offering faster turnaround times, while others may prioritize customization, leading to extended projects. The experience level and reputation of the builder are important factors influencing the efficiency and accuracy of their estimated timelines. Builders with a proven track record and established processes may deliver projects within the projected timelines more consistently.
Typical Construction Times Table
Tiny House Size (sq ft) | Construction Method | Builder Experience Level | Estimated Construction Time (weeks) |
---|---|---|---|
150-250 | Prefabricated Panels | Experienced | 8-12 |
250-350 | Site-built with SIPs | Intermediate | 12-16 |
350-450 | Custom Design with Wood Framing | Experienced | 16-24 |
450+ | Custom Design with Metal Framing | Expert | 24+ |
This table provides a general guideline. Actual construction times may vary based on specific project requirements and unforeseen circumstances. The estimated timeframes are based on average industry practices and are not guarantees. Factors like permit acquisition, material availability, and unexpected complications can impact the overall duration.
Construction Methods and Processes
The construction of a tiny house, while potentially simpler than a traditional home, requires meticulous planning and execution. Careful consideration of materials, techniques, and processes is paramount to achieving a structurally sound, energy-efficient, and aesthetically pleasing dwelling. Different approaches to framing, insulation, and finishing can significantly impact the final product.Common methods and processes in tiny house construction involve a range of techniques.
Frame construction, for instance, can utilize pressure-treated lumber, laminated veneer lumber (LVL), or even metal framing, each offering varying degrees of strength, cost, and aesthetic appeal. Insulation strategies often incorporate rigid foam board, spray foam, or cellulose fiber, influencing the home’s thermal performance. Exterior and interior finishes can be tailored to the desired aesthetic, with options including vinyl siding, wood cladding, or various paint and stain choices.
Framing
The framing process is foundational to the tiny house structure. It dictates the overall strength and stability of the dwelling. Common techniques include platform framing, where the framing is built on a level platform, or post-and-beam framing, utilizing vertical supports and beams. The chosen method impacts the interior layout and the overall design. Careful consideration of load-bearing walls, joists, and rafters is critical.
Properly sized and installed structural components are essential to ensure the long-term integrity of the tiny house.
Insulation
Insulation is critical for maintaining a comfortable interior temperature and reducing energy consumption. Common methods include using rigid foam boards, often adhered to the exterior walls and the ceiling. Spray foam insulation is another popular choice, offering excellent sealing and insulation value. The choice of insulation method depends on factors such as budget, desired R-value, and the overall construction approach.
Water Systems
Tiny house water systems often involve compact fixtures and efficient plumbing. Greywater systems, collecting water from sinks and showers, are increasingly common to reduce wastewater discharge. The selection of water heaters, storage tanks, and pipes is crucial to ensure adequate water pressure and minimize leaks. Proper sizing and placement of water fixtures are critical for maintaining efficiency.
Electrical Systems
Electrical systems in tiny houses need to be designed to accommodate the specific needs of the dwelling. This often involves careful planning to avoid overloading circuits and ensure safety. The choice of wiring, outlets, and lighting fixtures directly impacts the home’s functionality and safety. Proper grounding and circuit breakers are crucial safety features.
Finishing
Exterior and interior finishes are vital to the tiny house’s aesthetic appeal and durability. Exterior options include siding, paints, and sealants. Interior choices often involve flooring, wall coverings, and cabinetry. Finishing materials should be chosen for their durability, moisture resistance, and aesthetic appeal.
Construction Process Steps
Step | Description | Estimated Time (days) |
---|---|---|
Design and Planning | Creating blueprints, selecting materials, and obtaining permits. | 5-10 |
Framing | Constructing the structural frame of the tiny house. | 10-15 |
Insulation | Applying insulation to walls, roof, and floor. | 5-7 |
Plumbing and Electrical | Installing water and electrical systems. | 7-10 |
Exterior Finishing | Completing exterior finishes like siding and paint. | 3-5 |
Interior Finishing | Installing interior features like flooring, cabinets, and countertops. | 5-7 |
Final Inspections and Completion | Final inspections and any necessary repairs. | 2-3 |
Impact of Design Choices on Time
Design decisions significantly impact the construction timeline of a tiny house, influencing everything from initial planning to final finishing touches. Careful consideration of features and customization levels is crucial for accurate time estimations and successful project completion. The complexity of the design directly correlates with the time investment required.Design complexity directly impacts the time required for construction. Detailed specifications, unique architectural elements, and the inclusion of intricate features all contribute to extended construction durations.
Conversely, a streamlined design with fewer features and readily available materials can expedite the building process. Careful pre-planning and a well-defined scope of work are essential to manage expectations and avoid unexpected delays.
Impact of Specific Features
The inclusion of specific features significantly influences construction time. For instance, a custom kitchen design with intricate cabinetry, specialized appliances, or unique layout demands more time for design, material procurement, and installation compared to a standard kitchen design. Similarly, incorporating a large, custom-designed window or skylight will require more time for precise fabrication and installation. The design complexity for the bathroom, including features like a shower, bathtub, or specific fixtures, also impacts the timeframe.
The availability of pre-fabricated components or modular systems can, however, streamline the process.
Impact of Unique or Custom Design Elements
Unique or custom design elements often introduce delays. These elements may involve intricate structural modifications, custom-built components, or non-standard material choices. Custom windows, doors, or furniture require specialized fabrication and installation, which invariably increases construction time. Furthermore, unusual material selection, like rare woods or exotic metals, may prolong the project due to sourcing challenges. Conversely, the use of readily available and standardized components can expedite the process.
Potential Time-Saving Strategies
Careful planning and pre-fabrication can significantly reduce construction time. Developing detailed blueprints and specifications upfront can prevent costly revisions and delays. Employing pre-fabricated components or modular systems can also reduce on-site construction time. Prioritizing quality control throughout the construction process is crucial, but shortcuts in quality control can jeopardize safety and structural integrity, so these should be avoided.
Employing experienced and skilled craftsmen with a proven track record of timely and efficient work is another time-saving strategy.
Comparison of Construction Time for Basic vs. Feature-Rich Tiny Houses
Feature | Basic Tiny House (Days) | Tiny House with Multiple Features (Days) | Additional Work (Hours/Day) |
---|---|---|---|
Basic Structure | 15-25 | 15-25 | 0 |
Standard Kitchen | 5 | 10 | 5 |
Custom Bathroom with Shower | 5 | 10 | 5 |
Custom Windows & Doors | 2 | 5 | 3 |
Solar Panel Installation | 2 | 2 | 0 |
Total Estimated Construction Time | 29-37 | 57-67 | (Variable) |
This table provides a general comparison. Actual construction times can vary depending on specific site conditions, weather patterns, and the chosen construction methods. The additional work column estimates the time spent on each feature, and the total estimated construction time is a rough guide, not a fixed number.
Estimating Costs and Time
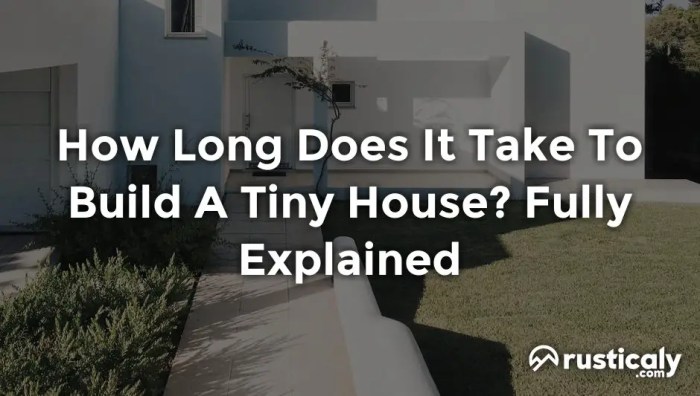
Accurately estimating the cost and timeframe for tiny house construction is crucial for successful project planning. A meticulous approach considers variables such as size, desired features, chosen materials, and local regulations. Understanding these factors enables realistic budgeting and helps avoid costly delays.A comprehensive estimation process encompasses both the direct costs of materials and labor, and the indirect costs associated with permits, inspections, and potential unforeseen issues.
Careful consideration of these elements ensures a project stays on track financially and temporally.
Cost Estimation Methodology
A reliable cost estimation method involves breaking down the project into manageable components. Firstly, define the precise size and features of the tiny house. This includes square footage, number of rooms, desired amenities (e.g., bathroom, kitchen), and any specialized features. Secondly, research and gather pricing information for materials, including lumber, insulation, windows, doors, and appliances. Thirdly, determine labor costs based on local market rates and the complexity of the project.
This often includes framing, roofing, plumbing, and electrical work. Finally, estimate costs for permits, inspections, and any potential unforeseen expenses. Using a detailed breakdown facilitates a comprehensive budget that is adjusted as the project progresses.
Impact of Size and Features on Costs
The size and features directly impact the cost and time required for construction. A larger tiny house with more complex features, such as a bathroom or a dedicated workspace, necessitates more materials, labor, and potentially specialized expertise. Conversely, a smaller structure with basic features will likely have a lower cost and a shorter construction timeline. For example, a tiny house exceeding 400 square feet with a fully equipped kitchen, bathroom, and a custom-designed interior will significantly increase both material and labor costs compared to a smaller model with basic amenities.
Impact of Materials on Costs
The choice of materials has a substantial impact on both cost and construction time. Premium materials, such as high-quality lumber or specialized insulation, can increase the initial investment but potentially reduce long-term maintenance costs. Conversely, using readily available, lower-cost materials may require more time and effort during construction. For example, using recycled or reclaimed materials could lead to a lower cost but might require additional effort in preparation and fitting.
Role of Permits, Inspections, and Regulations
Permits, inspections, and regulations are critical factors in determining the overall project duration. The time required for obtaining necessary permits and navigating local building codes can vary significantly depending on the jurisdiction. Delays in securing approvals can lead to project delays and unexpected cost increases. Furthermore, inspections conducted at various stages of construction ensure compliance with regulations, preventing potential setbacks or costly rework later in the project.
Estimating Construction Time
Estimating construction time requires careful consideration of the project’s complexity and the availability of skilled labor. A simple tiny house with standard features might be completed in a few weeks, whereas a more complex design with specialized features could take several months. This time estimate also accounts for potential delays caused by material sourcing, unforeseen issues, or weather conditions.
Cost and Time Estimation Table
Factor | Impact on Cost | Impact on Time |
---|---|---|
Size of Tiny House | High | High |
Features (e.g., bathroom, kitchen) | High | High |
Materials (e.g., lumber, insulation) | Moderate to High | Moderate |
Labor Costs | High | High |
Permits and Inspections | Low | High |
Unforeseen Issues | High | High |
Troubleshooting Potential Delays
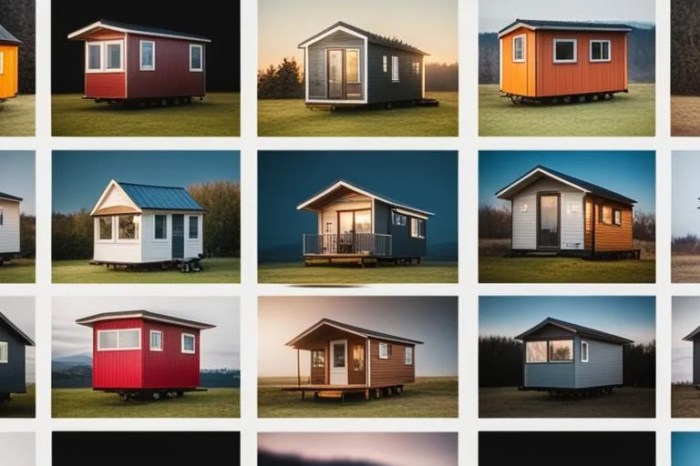
Tiny house construction, while often lauded for its efficiency, is susceptible to unforeseen circumstances that can disrupt timelines. Careful planning and proactive problem-solving are crucial to mitigate these delays and maintain project integrity. Addressing potential issues head-on can save significant time and resources.Unexpected challenges, such as material shortages or adverse weather conditions, can significantly impact project timelines. Developing contingency plans and establishing strong communication channels with vendors and subcontractors are vital to navigate these situations effectively.
Understanding how different builders address these hurdles can offer valuable insights.
Material Shortages and Supply Chain Disruptions
Anticipating and mitigating material shortages is paramount. Builders must maintain robust relationships with suppliers, ensuring timely delivery and sufficient stockpiles to buffer against potential delays. Regular communication with suppliers about projected demand and potential disruptions is essential. Monitoring market trends and alternative material options can help reduce reliance on single sources. Some builders maintain multiple supplier relationships, allowing for substitutions if one source experiences delays.
For example, a builder might have backup suppliers for specific lumber types or specialized components, reducing the impact of a single supplier’s issues.
Unexpected Weather Events
Adverse weather conditions can halt or significantly slow construction activities. Project schedules should incorporate buffer time for potential weather delays, especially in regions with unpredictable climates. Builders should establish clear protocols for weather-related postponements, ensuring that workers and subcontractors are informed and prepared. Contingency plans for workarounds, such as using covered areas for indoor work, can minimize the impact of unforeseen weather.
Constructing a tiny house, a testament to mindful living, often unfolds over several months, mirroring the deliberate pace of creation. The journey, much like the exquisite culinary artistry of a fine restaurant like restaurant italien québec ste foy , requires careful consideration and meticulous craftsmanship. Ultimately, the duration hinges on individual design choices and the inherent rhythm of the building process, culminating in a harmonious sanctuary.
Construction companies often use weather forecasting tools and have experience with local climate patterns to adjust their schedules and prioritize tasks that are less susceptible to weather interruptions. For instance, framing can often be postponed if necessary and completed indoors.
Unforeseen Design Changes or Modifications
Design modifications, while sometimes desirable, can introduce unforeseen delays. Clear communication protocols should be established with clients to address any changes early in the project. Detailed design specifications and comprehensive blueprints can minimize the chance of ambiguity and subsequent delays. Experienced tiny house builders often use collaborative design software that allows clients to visualize and adjust design options before construction begins, reducing the number of changes during the actual construction process.
Table of Potential Problems, Causes, and Solutions
Potential Problem | Causes | Proposed Solutions |
---|---|---|
Material Shortages | Supply chain disruptions, unexpected demand, supplier issues | Maintaining multiple supplier relationships, stockpiling materials, monitoring market trends, exploring alternative materials |
Unexpected Weather Events | Severe storms, prolonged periods of rain, extreme temperatures | Buffer time in schedules, clear protocols for weather-related delays, utilizing indoor workspaces, contingency plans |
Unforeseen Design Changes | Client requests, design revisions, unforeseen site conditions | Clear communication protocols with clients, comprehensive design specifications, collaborative design software, early design reviews |
Last Word: How Long Does It Take To Build A Tiny House
In conclusion, the time required to build a tiny house is a multifaceted equation, determined by individual choices and circumstances. While estimates provide a framework, the actual duration can vary widely, highlighting the unique nature of each project. The meticulous planning and execution of every detail ultimately dictate the length of this remarkable journey into a smaller, yet fulfilling, lifestyle.
Query Resolution
How much does a tiny house cost?
Costs vary greatly depending on the size, features, materials, and location. Detailed cost breakdowns are essential to manage expectations.
What are the most common materials used in tiny house construction?
Plywood, steel, and treated lumber are prevalent choices, but sustainable and alternative materials are increasingly used.
Are there any special permits or regulations for tiny houses?
Local zoning regulations and building codes often differ for tiny houses, and understanding these regulations is crucial for a smooth process.
How do prefabricated tiny houses differ from custom-built ones in terms of time?
Prefabricated tiny houses often have shorter construction times due to standardized components and pre-assembly, while custom builds allow for more personalized design but can take longer.